On January 28th, 1986, the Challenger launched from Cape Canaveral, Florida, for what was the 25th orbital mission of the Space Shuttle program. 59 seconds after launch, a tracking camera recorded a burning plume coming out of the side of the right solid rocket booster (SRB). As the leaking fuel continued to burn, gradually other parts of the shuttle stack began to disintegrate. 73 seconds after launch, still visible in the sky, the shuttle exploded as different fuel sources ignited. This was particularly shocking both for being the first American astronaut deaths in a launch mission*, as well as its public broadcasting as part of the inaugural Teacher in Space Project.
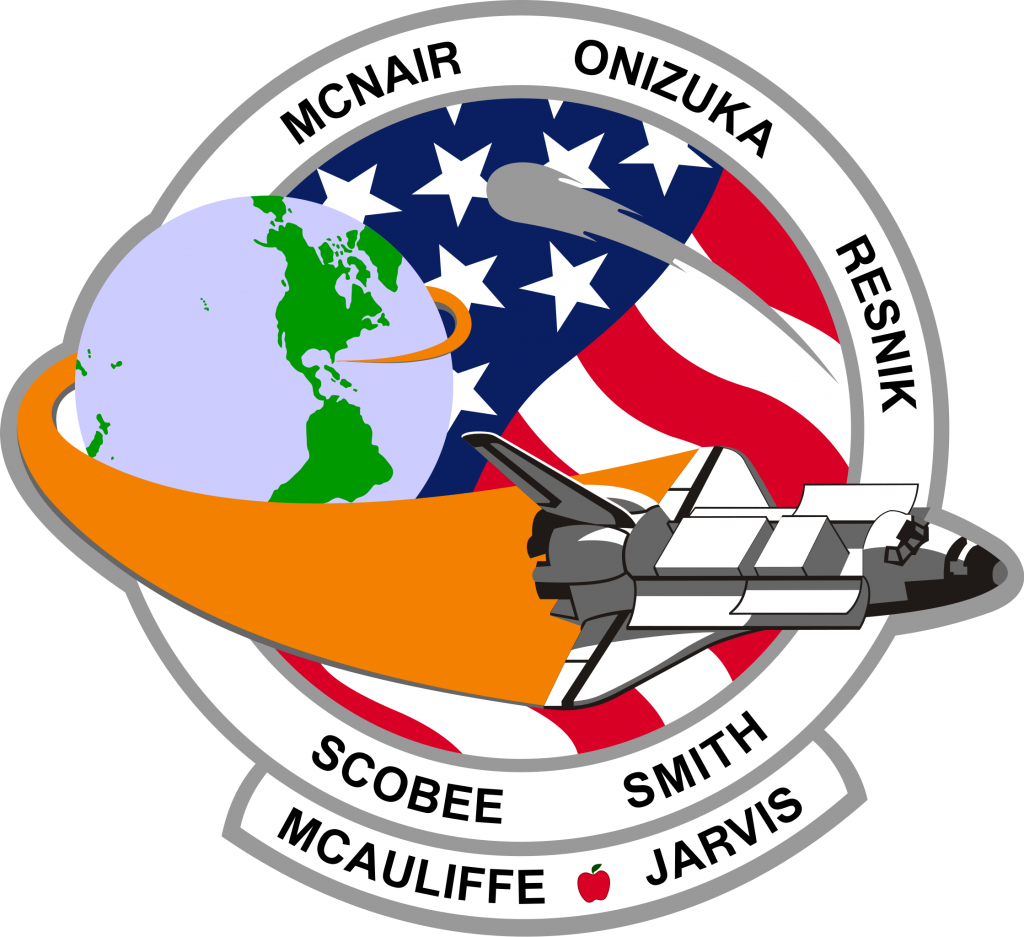
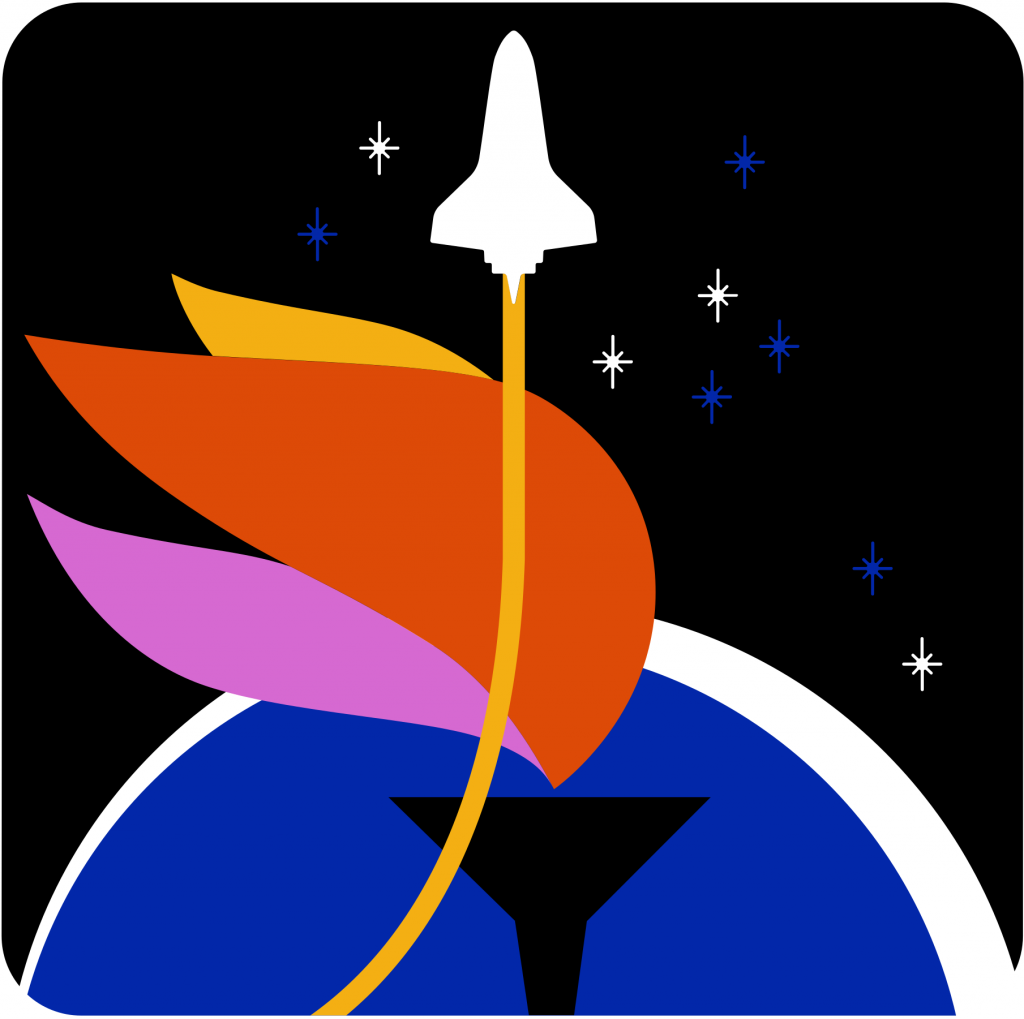
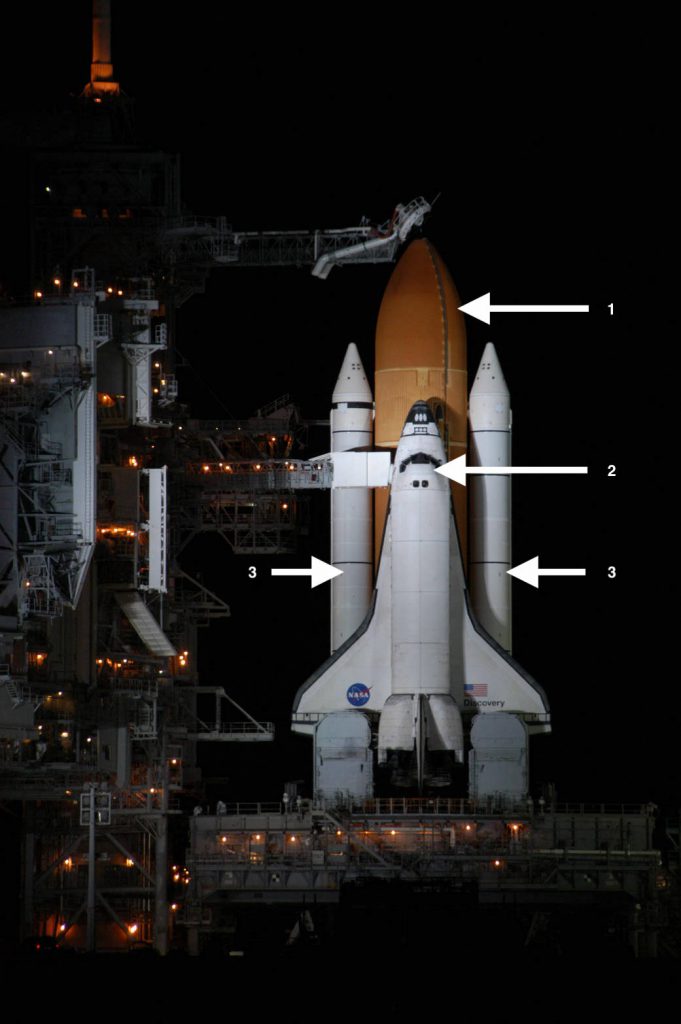
Like many other applications, the SRBs’ O-rings sealed against gas to prevent it from escaping where mechanical joints connected. Every Shuttle launch required 2 SRBs, with each SRB containing 3 field-joints that used O-ring seals. For redundancy, each field-joint had both a primary and a secondary O-ring. This resulted in 6 field-joint O-rings total per SRB, or 12 field-joint O-rings total per launch.
Redundancy is needed because of the potential for an O-ring to fail. There are two mechanisms which could cause this, known as erosion and blow-by. Erosion has the potential to occur during normal operation, where hot gases sealed against the O-ring gradually disintegrate it. On the SRBs, putty was added to provide a protective barrier against this mechanism. Blow-by occurs when an O-ring already fails to provide a complete seal, allowing high velocity gas to move past the O-ring and damage it further.
Being made of rubber-like material, there are a variety of conditions which may impact the ability of any O-ring to provide a complete seal. One which was investigated for the Space Shuttle program was temperature, where colder conditions can cause an O-ring to shrink and lose its elasticity. During the late 1970s and early 1980s, the SRB engine with the O-rings was qualified for temperatures as low as 40°F.
Without any additional statistics, when the Challenger started its Winter morning launch it was 36°F.
*Apollo 1 resulted in 3 astronaut deaths during pre-launch training on the ground. Soyuz 1 and 11 resulted in a combined 4 cosmonaut deaths due to hardware failures during each launch mission.
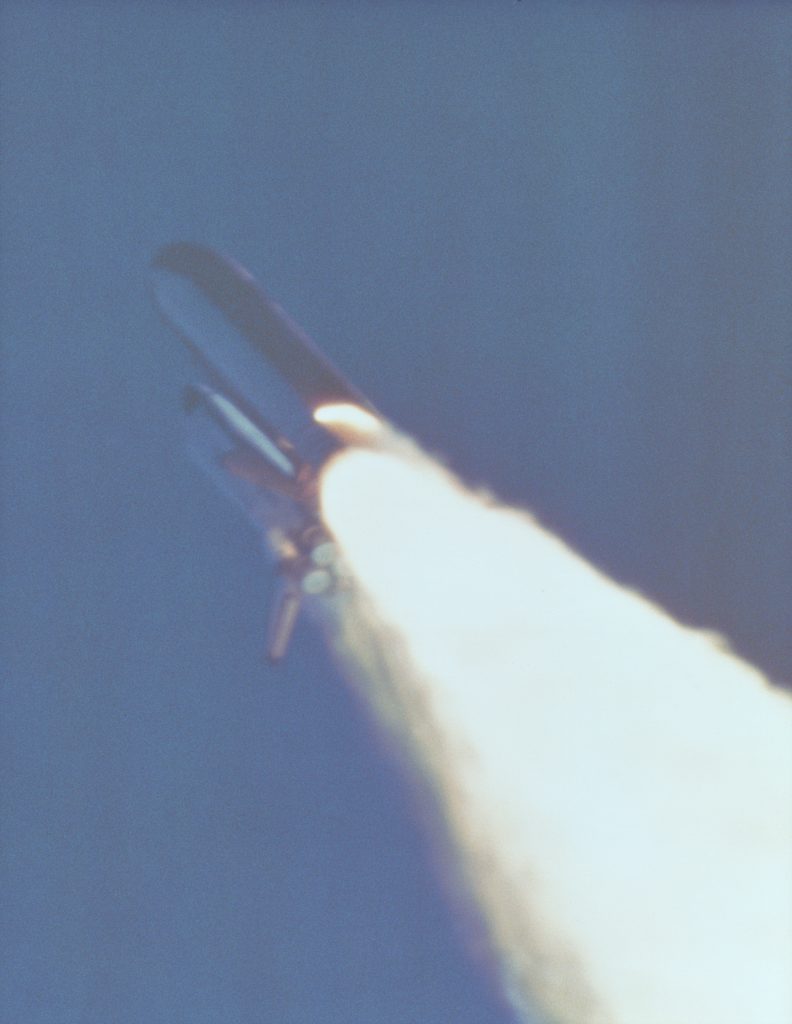